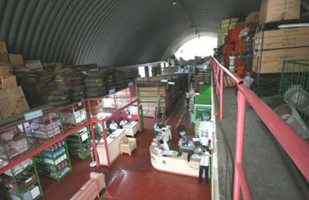
Centralized Warehousing Management System
Marikina City
2008
While the trend in government service delivery has been decentralization, Marikina City undertook the opposite track (at least in supply management!) in 2002 and seems to have attained more efficient delivery of services as well as cost savings since then.
Apparently, after making a critical assessment of the way it has been doing things, Marikina’s local administration concluded that decentralized supply management has become impractical with respect to cost, space and time components. There were roughly 45 departments with a total of 135 personnel engaged in supply bidding, procurement and management, which entailed a labor cost amounting to a minimum of P9.5 million a year. This amount does not include the equipment cost of P697,500 for the operation of the various stockrooms, the rental cost for storage space of P200 to P300 per square meter, nor the possible cost of purchasing storage lots amounting to P5,000 to P10,000 per square meter. The Marikina administration also learned that project implementation would be greatly hastened if they have supplies on hand that they could put to immediate use.
Thus, Marikina’s local government established a 900 square meter Central Warehouse containing supplies such as lumber, paint, bolts, nails, electrical components as well as office and school supplies and equipment. It even houses disaster and relief goods. The mechanics and systems of the best private warehouses as well as leading hardware enterprises in the country were adopted and put in place with some modifications. In centralizing supply management, the supply chain is handled by one department tasked to monitor, inventory, deliver and inspect the proper use and distribution of materials to end users and project sites.
By introducing the advanced withdrawal concept, the various project implementing departments could immediately obtain the materials they need from the central warehouse while at the same time undertake the public bidding of replacement materials that would replenish the stocks at the warehouse. This way, the implementing department could immediately proceed with the completion of projects such as the repair or construction of roads and still comply with the law on public bidding.
To properly cope with demand, the central warehouse is stocked with supplies that conform to the trend analysis of the consumption of items by various end users during different seasons. This means that the warehouse’s inventory of materials could cover peak requirements like construction materials for the summer season, lifesaving gadgets and relief goods during the rainy season, decorative materials for events during festivities as well as school supplies and materials during the school season.
The Central Warehouse has a bar coding system and wide area network (WAN) in place which enables it to make a quick inventory as well as properly and quickly release supplies and materials. The mayor can even inspect the inventory of supplies online. This computerized system allows the strategic positioning of fast moving items vis-à-vis slow moving items. It also provides objective information for management decisions such as the determination of priority purchases of materials and supplies. The system also provides a better safeguard against pilferage as it enables close monitoring of the proper use of the materials and the retrieval of excess materials from the finished projects. Hence, wastage is reduced or even eliminated.
With the central warehouse in place, the number of personnel engaged in supply administration was reduced to only 34, which also reduced labor costs to roughly only P2.4 million yearly. The city did not need to hire additional personnel as the General Services Office was tapped to manage the warehouse. Office equipment cost was also reduced to between P50,000 and P100,000. And since the warehouse was ordering supplies in bulk instead of on a per item basis, the cost of materials was also obtained at a discount.
With the implementation of RA 9184, the City Government also generated savings through competitive public bidding for all its projects, supplies, and materials. From January to November 2007, the City Government of Marikina had 414 work programs with a projected cost of roughly P391 million that were subjected to public bidding. After the bid evaluation, the total aggregate amount was approximately P375 million, which translated to a savings of roughly P16 million for the city.
Admittedly, the people’s participation and empowerment is indirect. But their awareness of the needs of their communities was sufficient to drive the city administrators to deliver basic services promptly. With the availability of materials stocked at the Central Warehouse, the project requests from the communities were being addressed expeditiously. Service without delay became the battle cry of the city.
Clearly, the establishment of the Central Warehouse has led to the effective and efficient distribution and utilization of supplies and materials by the city government. It is also proving to be a wise investment for maximizing growth, developing cutting-edge strategies and securing a better future.
Marikina City has a policy of sharing its best practices with other local government units. To date, the provinces of Quirino, Batangas and Guimaras and some LGUs from the National Capital Region have consulted the city about its Central Warehousing Operations. Hopefully, they would also be able to replicate the program in their respective domains and begin delivering services more promptly and more efficiently.